これがなければ、今日の携帯電話普及は… |
「もっと高速化、高精度。他社が追随できないレベルを追求し続ける」と開発チーム代表の高橋さんが言う。従来のビアホール加工600穴/秒から最大4500穴/秒、7.5倍ものプリント基板穴あけレーザー加工機の飛躍的高速化を達成した技術のことである。今日、例えば携帯電話が、日を追って高機能化すると同時に小型化している一番の決め手は、限られたスペースの中に複雑な電子回路を形成する技術、すなわちプリント基板の高密度化であり、それは数層に積み重ねた回路パターンの層間を穴径0.05〜0.1mmの微細な導通穴=ビアホールで接続するビルドアップ基板によって実現してきた。基板1枚あたり(600×500mm相当に約50台分の回路パターン)のビアホール数は1998年に約3万穴だったものが、今日では20万穴以上に及び、さらに増加の一途をたどっている。その一方で全世界の携帯電話生産台数は1998年の1.8億台が、2010年には約12.5億台へと増大が見込まれるに至っている。まさにこのビアホール加工の高速化技術による生産性の向上がなければ、これは実現し得ない規模といって過言ではない。
|
事業化2年で、加工法のスタンダードに |
三菱電機がビルドアップ基板へのレーザーによる穴あけ加工に取り組みを開始したのは1980年代後半のことである。当時はドリル穴あけやエッチング加工が主流で、「微細穴へのニーズも低く、お客様であるプリント基板メーカーさんにはまったく見向きもされなかった」(名古屋製作所・竹野祥瑞さん)という状況だった。
しかし1995年、開発チームはレーザーによるビアホール加工技術を確立。1996年、レーザー発振器から出力されたレーザービームを、2個1組のガルバノスキャナとfθレンズによりプリント基板に位置決め照射して加工するプリント基板穴あけレーザー加工機を製品化、その製作・販売を事業として立ち上げた。これはちょうど世界的に携帯電話の小型化に拍車がかかる時期にあたり、速く正確に微細穴加工が可能なこのレーザー方式は数年後には、ビルドアップ基板のビアホール加工のスタンダード工法として従来工法に取って代わったのである。
|
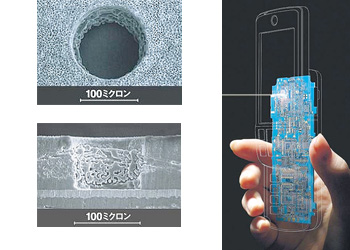 |
携帯電話のプリント基板にあけられたレーザー加工のビアホール。 後工程でホール内に銅めっきを施し、回路パターンの層間を接続する |
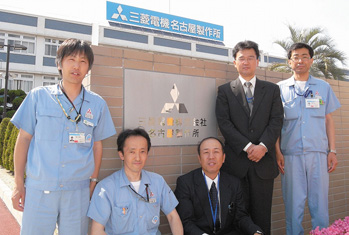 |
右から開発チームを代表して市村産業賞功績賞を受賞した鉾館さん、小林さん、高橋さん
左から事業立ち上げ時から中心メンバーとして加工機高速化を推進した竹野さん、黒澤さん |
|
生産基盤確立と、国際競争力強化のためにも |
開発チームの目は、単に他に優る加工機の開発に止まらず、わが国のIT機器分野での高付加価値製品生産基盤確立と国際競争力強化へと向けられた。そのキーワードが高生産性と低コスト。携帯電話、パソコン、デジタル家電等々の普及、高機能化と相まって、限られた時間の中でのより微細・高品質・大量加工への挑戦である。それは2000年以降、高速ガルバノスキャナを開発・高精度化した高橋さん、鉾館さん、光学系とビアホール加工品質担当の小林さん、レンズ・ミラー開発に携わった竹野さん、レーザー発振器と加工機生産技術を確立した名古屋製作所・黒澤満樹さん他、多くのメンバーにより加速されていった。
そして2008年、初期の加工機に対し、「レーザービームを4分割し、4穴同時加工を実現した光学系」、「4本のレーザービームを高速に位置決めするデジタルガルバノスキャナシステム」、「ガルバノスキャナのスキャンエリアを拡大した大面積fθレンズ」、「高速加工を実現する大出力CO2レーザー発振器」の開発による、微細ビアホールを最大4500穴/秒加工可能な2ヘッド2ワークのプリント基板穴あけレーザー加工機・ML605GTF-5150Uが完成した。
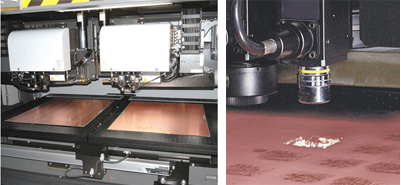 |
プリント基板穴あけレーザー加工機によるビアホール加工。右のアップ写真で
回路パターン層を接続するビアホールを加工する火花が見られる |
|